Inventory management metrics to handle demand volatility
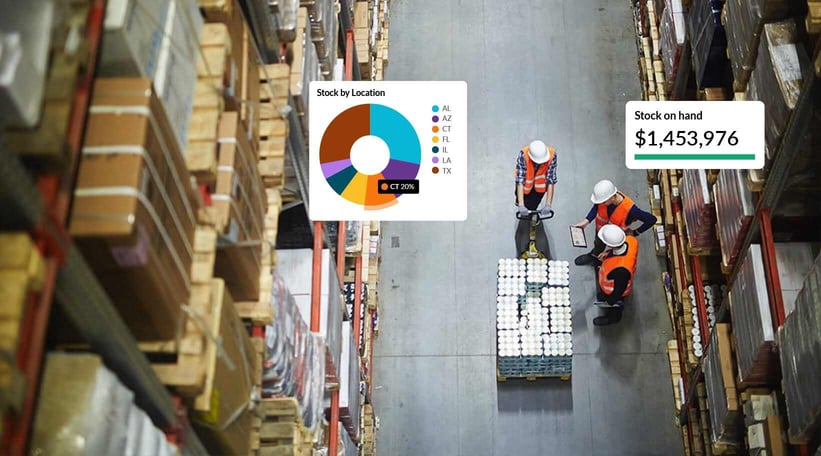
Navigating the global supply chain is rocky with demand volatility amplified by new tariffs and ongoing inflation. Businesses find themselves caught in a precarious balance, needing to maintain adequate inventory to meet customer demands while simultaneously operating in a demand-driven manner to minimize the burden of carrying excess stock. In this volatile landscape, relying on gut instinct is a recipe for disaster. Instead, a data-driven approach, centered on closely monitored inventory metrics, becomes the essential safeguard for managing uncertainty.
What is demand volatility?
Demand volatility refers to unpredictable and rapid changes in consumer demand for a product. It occurs when demand spikes or drops unexpectedly due to external factors such as economic conditions, consumer behavior shifts, or global events.
An example of demand volatility is the infamous Covid 19 toilet paper shortage, which occured in the early stages of the COVID-19 pandemic. In early 2020, as governments announced lockdowns and restrictions, consumers panic-bought essential goods, including toilet paper. This led to a sudden, extreme spike in demand that manufacturers and retailers were not prepared for.
A rigid supply chain planning approach, which expected stable demand, meant manufacturers couldn’t quickly scale up production or shift supply from commercial to consumer markets.
What causes demand volatility?
Demand volatility can be caused by any number external factors, some harder to predict than others:
-
Seasonality – Changes in demand patterns due to seasons, holidays, or weather.
-
Economic Factors – Recessions, inflation, or market booms affecting consumer spending.
-
Trends & Consumer Preferences – Shifts in tastes, technology, or social trends.
-
Supply Chain Disruptions – Raw material shortages, transportation issues, or geopolitical events.
-
Competitive Actions – Promotions, new product launches, or price wars.
-
Regulatory Changes – Government policies or trade regulations impacting demand.
With all these external pressures on businesses it’s clear that volatile demand is a factor that can impact inventory levels at any point.
Can demand volatility be measured?
Historical data can be used to calculate how much stock levels vary using the coefficient of variation (CV) calculation.
Coefficient of variation as a measure of volatility
CV = standard deviation / mean
Standard deviation measures how dispersed your data is compared to the mean; a low standard deviation means that stock levels matched demand more closely, whereas a high standard deviation indicates greater demand variability.
For example, Electrical Distributor A is tracking the stock levels of switches with a mean weekly count of 1100 and a standard variation of 500 has a CV of .45
Retailer B tracking the same switches over the same period had a mean weekly count 950 and a standard deviation of 375, and a lower CV of .39
This tells us that Retailer B is doing a better job at demand planning than Electrical Distributor A. Additionally a distributor can use their CV to better predict their forecast accuracy for future demand plans.
Strategies for volatile markets
While an extreme example of demand volatility, the “great toilet paper shortage” demonstrates the challenges and unexpected demand fluctuations can throw at manufacturers, wholesalers and distributors. It has encouraged companies to adopt better demand forecasting models, diversify suppliers, and improve inventory optimization strategies to reduce the risk of similar shortages.
And now with global tariffs, continued high interest rates and inflation these same businesses are being asked to manage inventory levels prudently. Some current inventory strategies we suggest for these market trends include:
1. Keep a close eye on cashflow
Automated cash flow reporting gives distributors a powerful competitive edge, especially when adapting to sudden shifts in consumer demand or economic shocks. With real-time visibility into their cash position, distributors can move faster than competitors—securing additional inventory from new suppliers, negotiating better payment terms, or obtaining short-term credit before market conditions change. This agility ensures they can meet surging demand or pivot during downturns without financial strain, while less-prepared rivals struggle to react. By automating the reporting of cash flow, distributors not only safeguard operations but also position themselves as reliable partners, ready to seize opportunities and out manoeuvre the competition.
2. Get an early warning of stockouts
As everyone knows, not having sufficient stock on hand leads to lost sales. When customers aren’t able to acquire the products they need, they seek out a competitor who does. Where demand is strong, you might need to pursue alternative sourcing strategies to continue to meet customer demand, or when stock is hard to obtain, it is best to prioritize your regular customers.
Tracking inventory KPIs is an effective way to determine how much stock is on hand and how long you can sustain the increased demand. While inventory management metrics may vary depending on the type of products or warehouse your company has, there are a few key measures that will help managers avoid stockouts.
3. Inventory turn and stock on hand
Knowing exactly how much stock you have on hand and when those items run out will help you to measure how well your company is moving inventory. In terms of inventory turnover, understock is represented by an excessively high inventory turnover ratio. In difficult market conditions, inventory safety stock levels may need to be updated to reflect the volatility of supply and demand. Some supply chain experts suggest businesses need to secure additional stock as a buffer to further disruption. Still if cash flow is tight – you need to be sure you are selecting the products that can sell or you can acquire these products for a reasonable price. With ad hoc data analytics, you can model the extra cost to buy (factoring in exchange rates, extra transport costs) and hold the stock and determine if it is viable before you make your decision.
4. Supplier lead times
Supplier lead time data is critical to procurement and replenishment planning. When demand patterns shift suddenly, lead times can fluctuate as other retailers rush to restock. If a supplier offers fast delivery, maintaining excessive inventory may be unnecessary. However, if a supplier has longer production schedules, frequent reordering may be required.
Delivery in full on time (DIFOT)
The DIFOT metric is an excellent way to measure your customer service. DIFOT is simply the number of orders that were delivered on time, with the right quantity of the correct products, on the day that the customer required them. During periods of demand variability, it's essential to monitor DIFOT scores and communicate any changes to customers so everyone can make informed decisions.
5. Watch out for excess inventory
Most trends emerge slowly, but when a ‘black swan’ event like COVID-19 happens, it can be tricky to manage. A sudden surge in demand sends a signal along the supply chain to increase production and demand forward may occur. This is called the bullwhip effect because as the demand wanes, it can lead to an overstock. In addition to lost capital, overstock wastes valuable space that more lucrative stock could occupy.
Using data to build resilient supply chains
Data analytics provides a 360-degree view of your operations. The ability to see constraints in real-time allows you to develop contingency plans. By extracting information from your disparate data storage silos and funneling into a centralized repository, managers can keep an eye on metrics related to inventory automation. Using data analytics to optimize inventory, you can evaluate the viability of buffer stock, keep customers informed and manage profitability.

Empowering businesses with intuitive data analytics, driving informed decisions for growth and profitability. We make people feel good about data.
Related blog posts
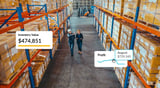
The U.S. wholesale distribution sector is experiencing a rapid acceleration in mergers & acquisitions (M&A) activity. From HVAC buying groups like Johnstone Supply acquiring independents, to family-owned distributors selling due to succession challenges, consolidation is reshaping the distribution landscape. One recent example is Hein Electric Supply's acquisition of Laser Electric Supply highlights how strategic buyers are capitalizing on opportunities across the middle market.
Read more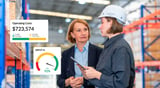
The Spring 2025 Fortune/Deloitte CEO Survey presents a consistent story of boardrooms experiencing a sense of cautious optimism controlled by an emphasis on fiscal responsibility. This is playing out with 42% of CEOs saying they want their teams to focus on cost-cutting measures without raising prices to avoid losing their customers.
Read more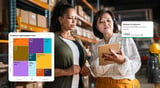
Most wholesale companies have access to sales data. Chances are you review sales weekly by variables like sales rep or product class. To make your sales efforts more effective, start by refining how you segment or group customers.
Read moreBrowse by category
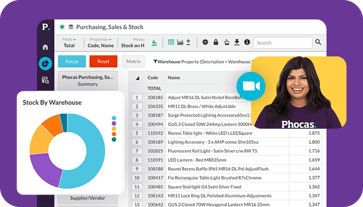
Find out how our platform gives you the visibility you need to get more done.
Get your demo today