ERPs for manufacturing - can they also handle FP&A?
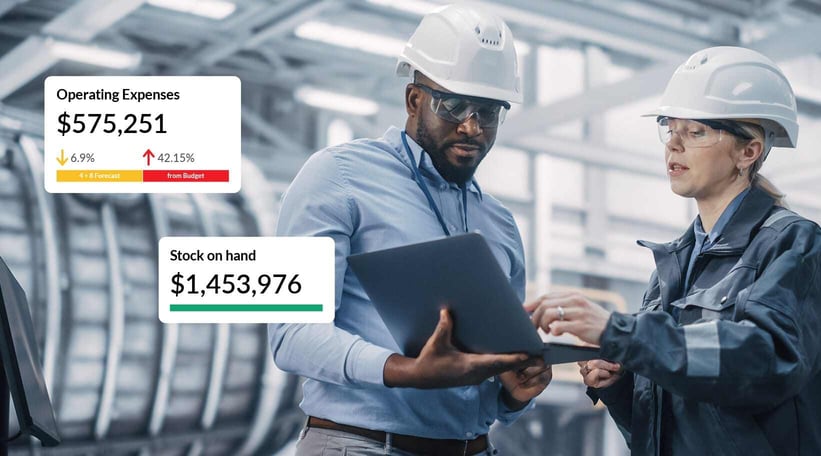
Just as every cog and gear must turn with precision to be viable, a manufacturer has another necessary business tool, the ERP. Manufacturing operations were offered a digital boost in the 90s when enterprise resource planning (ERP) software came into use and the software continues to be relied on today for end-to end manufacturing management.
What is a manufacturing ERP system?
ERP software streamlines operations and enhances efficiencies by measuring and improving how a company allocates its materials. The outcomes from using manufacturing ERP systems made a huge impact on the industry by allowing people to review manufacturing processes and find new ways to make the same products but do it faster and cheaper while maintaining quality control. These changes had a positive effect on profitability and growth so the ERP system caught on.
As the ERP systems can capture a vast amount of information about a manufacturing business there are also other benefits from using an industry-specific ERP system such as improving efficiencies across supply chain management, warehousing and transportation as well as improving compliance, managing the shopfloor workforce and providing a better customer experience.
Once these efficiencies were achieved, the ERP system was earmarked in a business to consolidate financial and operational information and provide real-time reporting about the business and it was hoped, the ERP could do it all, eliminating the need for multiple software systems that don’t integrate well with each other. Has full software market dominance been achieved by the ERP systems in manufacturing? We are not so sure but many manufacturing companies are certainly achieving strong business performance with the right tech stack.
The difference between a standard ERP and manufacturing ERP
There are many ERP systems available so its probably best to differentiate them as two distinct types, the standard (catch-all) and the industry specific (such as manufacturing ERP software). The standard ERP software is often a generic system with all the basic functionality but requiring heavy customization to suit specific needs. There is also manufacturing ERP software that is specifically designed for the manufacturing industry, offering sophisticated features to address industry-specific requirements. The manufacturing ERP system merges key business operations (sales, finance) with manufacturing procedures (warehouse management, bill of materials, procurement, production processes, production planning, order management and production scheduling), allowing more oversight and control of a manufacturing business.
Best manufacturing ERPs
The leading providers in manufacturing ERP solutions include Epicor, SAP, Sage, Microsoft Dynamics, Oracle, Infor and NetSuite. At Phocas, we have deep relationships with all the best manufacturing ERP solutions and know their systems well because our technicians have integrated business intelligence and financial planning software into these ERPs for 20 years.
Customization of ERP versus adding more software
Personalization and customization of software can be challenging. ERP platforms have hundreds of moving parts, and they all need to work together so when developers start to tinker with them - things can go wrong and get expensive. Manufacturers also need to know the exact requirements of the changes so they can relate to the developers and get the extra information they need. If your requirements are unclear, it makes managing a software development project much harder and there is a greater chance of error. You can imagine how this plays out and no doubt many of you have experienced customization projects going wrong.
When customization is required in an ERP especially when it relates to FP&A or BI functionality, it is often faster, cheaper and more reliable to add bespoke software. Again, you need to know what functionality you require or what your manufacturing software doesn’t allow you to do so that you can select software that compliments and integrates well with your ERP system.
The ERP system collates all the business data from human resources, inventory levels to sales orders but often the business users have trouble performing deeper analysis in the ERP platform. Often in a manufacturing ERP, the data is flat (not in a nested view) so people aren’t able to access multiple layers of detailed information. Usually static data is a key reason that people can’t do further analysis as they need to find out what is really happening beyond a primary or top layer view. They know all the data is the ERP system but people can’t get it out or they can get it out but the reports are restricted or the layouts are hard to change forcing them to export the data into Excel so they can analyze it and see things.
This is where Phocas FP&A and BI adds value by being able to consolidate, validate and automate all the ERP data plus multiple other data sources into one centralized platform. This means people in the manufacturing business can access data in real-time and it can be used to create financial statements, management reports or budgets and forecasts. The addition of FP&A and BI software also helps the finance team easily measure financial and operational drivers of the business so they can then be used to create detailed budgets.
Bespoke software for FP&A and business intelligence has benefits for manufacturing businesses
When the software has been designed specifically to do financial planning tasks then there is a myriad of tailored features that can be accessed out of the box.
In this section of the blog, we’ll compare financial reporting and budgeting and forecasting in a manufacturing ERP compared to doing this tasks in a bespoke FP&A plus BI platform that has proven ERP implementation.
Customizable reporting
Tailored financial reporting software offers the highest level of customization and flexibility. It can be specifically designed to meet the unique needs of a manufacturer, incorporating specific data sources, metrics, and dashboard preferences for your whole team.
ERP systems provide standard financial reporting structures and are generally less flexible compared to purpose-built software. ERPs generally don’t accommodate highly specialized reporting needs without additional development time and cost.
Skip excel spreadsheet wrangling
ERP systems typically have integrated financial modules that include budgeting functionalities. Budgeting in ERP systems links to other financial processes such as general ledger, accounts payable, and accounts receivable. However, it usually also requires manual manipulations in Excel which affects the accuracy of the numbers and is time-consuming.
Collaborate on budgets with ease
ERP systems can offer standardized budgeting templates but few have sophisticated workflows making collaboration difficult. Often the finance team use Google docs as a means to collaborate with other departments when budgeting out of an ERP. All the changes need to be added manually back to the budgets. This makeshift technique can get messy especially when lots of people are involved and things get missed by finance or the model breaks.
In bespoke software the master budget can be designed from scratch, allowing for more flexibility to suit your business. With Phocas you are rewarded for the time spent building a budget model in year 1 which enables easy roll forward and continual monthly reforecasting. When the budget period ends, the coming 12 months of data are already there.
Built-in workflows also enable more secure collaboration over the data which can be a huge help for specialized parts of the budget like sales forecasting. The workflows are managed by the budget owner enabling them to share specific information with the people who need to see it. They can also provide access for the business partner to check or change data and while this is taking place, the head of sales or operations has control of the data. Manufacturing ERP systems typically offer basic forecasting functionalities based on historical data trends. In Phocas with specialized analytics functionality built-in other sub-planning tasks are available like scenario planning, sales forecasting and demand planning. The performance of forecasting and analysis can also be affected by the overall data load within the ERP environment whereas a bespoke system can process much larger volumes of data.
FP&A software + manufacturing ERPs = a truly dynamic and flexible reporting and planning solution
Adding specific FP&A software to a manufacturing ERP offers more customization and flexibility to report across your business and detailed budgeting and analysis specific to the organization's needs. As markets change and businesses become more complicated to manage, most manufacturers will require the FP&A and BI software to connect people to data and plan adequately for the future.

Katrina is a professional writer with a decade of experience in business and tech. She explains how data can work for business people and finance teams without all the tech jargon.
Related blog posts
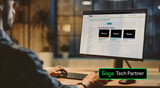
Phocas Software helps Sage customers gain more insights from their business Phocas Software, a business planning and analytics platform for sales, operations, and finance teams, announced a new technology partnership with Sage, the leader in accounting, financial, HR, and payroll technology. Phocas products are now integrated with Sage Intacct, making it easier for companies to access, analyze, report, and share information in their systems.
Read more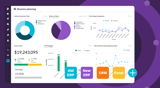
For many IT professionals, the thought of changing or updating an ERP system is unbearable. Aside from the selection process, which itself can take many months, the implementation project can run from a couple of months to a couple of years. During this period, existing IT infrastructure is generally put in a holding pattern and all new projects are frozen. So, how can business intelligence help streamline the transition and enhance your existing ERP solution?
Read moreBrowse by category
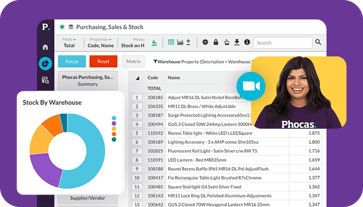
Find out how our platform gives you the visibility you need to get more done.
Get your demo today