5 trends in the building and industrial materials industry
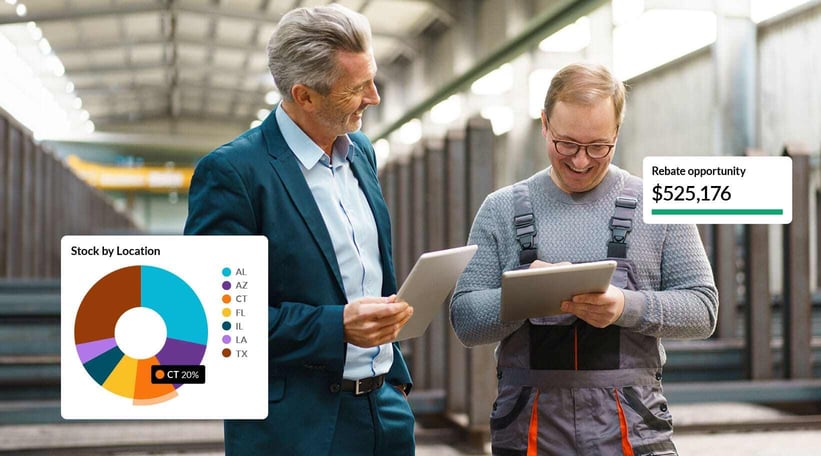
The building materials and construction industries are the engine room of the world making our homes, hospitals and hotels. The group represents 13 percent of global GDP. Despite high demand from the public and private sector, the industry has faced its own challenges post pandemic grappling with inflationary pressure, cashflow management and supply chain issues. We will explore five trends or advancements that are being adopted by the build materials and construction industry to manage change and ease these pressures.
Trend one – the high cost of building materials makes rebates essential
Until recently the construction industry had stable supply and demand but supply chain disruptions have caused raw materials to increase. Steel and timber prices have skyrocketed so construction companies that can keep margins under control or have a well-run rebate program with suppliers can protect the bottom line.
You need to have great partnerships with building materials suppliers so you can negotiate flexible pricing and set achievable rebate volumes. Clear visibility of all projects is also necessary with the most recent data available. Construction companies who invest in rebate management software to perform this analysis save both time and money, while avoiding costly pricing mistakes.
Trend two - increased digitization initiatives
Building materials and construction companies use a myriad of software with the main tools being Computer Aided Design (CAD) programs, Enterprise Resource Planning (ERP), Construction Management Software (CMS) and Business Intelligence and Financial Planning and Analysis (BI and FP&A). The BI and FP&A tools are proving helpful for companies to manage projects and show real-time aggregates of labor, use of advanced materials and emissions so projects can be managed in a sustainable, cost-effective way. These tools help finance teams reforecast or make clear decisions when they compare actuals with budgets.
Like all industries, many startups dedicated to solving the problems of the construction materials industry have emerged especially for eco-friendly materials, project management and energy efficiency.
Trend three - diverse employment polices to counter ongoing labor shortages
The building materials market is valued at USD 1.5 trillion and is expected to have compound average growth rate (cagr)of about 4% to 2030. The industry employs 9.2 million workers but labor shortages are being experienced globally, especially in the Asia Pacific. Many companies are successfully training women and new immigrants into roles and creating a steady pipeline of new talent. Attracting diverse talent is paramount for future durability as the construction industry workforce is also aging and a large proportion will retire in the next decade.
Trend four - modularity and prefabrication cuts construction project time
Prefabrication and modular construction is improving construction quality and sustainability as well as reducing construction project time. When parts of the build can be made off site there can be a number of advantages.
- The assembly-line process means younger tradespeople can be trained across all elements of the build.
- New sustainable building products can be tested.
- There is less waste reducing the carbon footprint of a build.
- The key benefit is the prefabrication keeps the project on time. Construction activities can take place simultaneously when raw materials are available and stored offsite until the main project is ready for them.
Trend five – a continued move to sustainability
Some governments encourage construction companies to meet carbon reduction targets and increase the use of renewable energy and energy efficiency technologies by offering financial assistance. For example, retrofitting existing buildings with products that increase energy efficiency is common in North America and Canada.
There is increased demand towards more sustainable buildings that have less ongoing environmental impact. Many companies are now making living materials such as bio-cement to reduce Co2 emisssions. These efforts aim to lessen the burden of waste on the planet. Sustainable materials such as recycled material and reclaimed wood also boost and allow for a circular economy.
Building materials and construction businesses can no longer afford to rely on outdated technologies or practices they’ve inherited through generations of family management. Getting started doesn’t have to be difficult. As a first step, you need to have full visibility into each project and determine what elements are working and those areas that are creating margin leakage. Fast access to business insights can be achieved with a BI and FP&A platform like Phocas.

Katrina is a professional writer with a decade of experience in business and tech. She explains how data can work for business people and finance teams without all the tech jargon.
Related blog posts
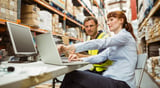
For the BMF's brand-new feature ‘Technology in Focus’ in their member magazine One Voice, they got the low-down from our very own Adam Butler; BI Consultant here at Phocas UK. Incase you missed it, here's his interview in full. Enjoy! Why is technology investment so important for the industry? In a highly competitive market like merchanting, technology can be a real source of competitive advantage for those willing to invest. Digital technology, such as BI and data analytics, can significantly improve business processes and drive long-term growth for branches, suppliers and customers.
Read more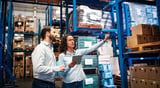
DIFOT (Delivered In-Full, On-Time) or OTIF (On-Time In-Full) is a fundamental KPI when analyzing the performance of your supply chain. The main goal is to get your customers the products they need, when they need them, in the quantity they ordered. DIFOT measures how successful your business is at achieving this objective and identifies procurement problems and supplier reliability.
Read more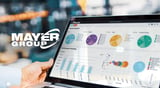
Phocas Software announces a new partnership with Mayer Group, a leading-edge IT firm and Acumatica Gold certified partner.
Read moreBrowse by category
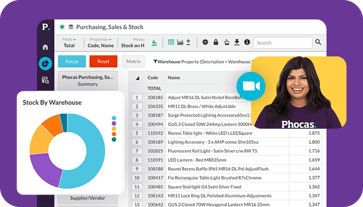
Find out how our platform gives you the visibility you need to get more done.
Get your demo today